钒铁精矿直接提钒(direct extraction of vanadium from ferro-vanadium concentrate)
钒铁精矿钠盐焙烧制取五氧化二钒的钒提取方法。又称铁精矿水法提钒。钒钛磁铁精矿经磨矿、磁选所得含钒铁精矿通常含V2O5O.5%~2%和全铁5O%~65%,可不经高炉炼铁和铁水吹钒渣而直接进行钠盐焙烧和水浸出提钒,提钒后的铁精矿再用作炼铁原料。
原理 经细磨的钒铁精矿和钠化剂(碱、芒硝或元明粉Na2SO4)制成粒或造成球,在焙烧炉内进行氧化钠化焙烧,钒铁精矿中的钒便被氧化生成V2O5:
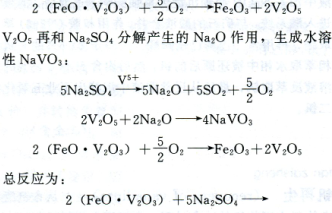

用水浸出焙烧产物过程中,NaVO3进入溶液与大部分不溶产物分离,然后再从经净化处理过的含钒溶液中沉淀出钒的化合物。
工艺 根据钠化焙烧所用的主体设备,钒铁精矿直接提钒又分为竖炉钠化焙烧、流态化床钠化焙烧、回转窑钠化焙烧和链算机回转窑钠化焙烧四种方法。
竖炉钠化焙烧提钒 芬兰劳塔鲁基(Rautaruukki)钢铁公司所属的奥坦梅基(Otan m äki)钒厂和木斯特瓦拉(Mustavaara)钒厂均采用钒铁精矿加钠盐造球,竖炉钠化焙烧的提钒方法。奥坦梅基钒厂所用的原料成分(质量分数ω /%)为:全Fe68.4,TiO23.2,V2O51.125,SiO2O.4,CaOO.O6,MgOO.24,A12O3O.5。钒铁精矿磨至-O.O38mm粒级占85%,加入占料量2.2%~2.3%的芒硝(Na2SO4)或1.6%~1.8%Na2CO3,用混料圆筒(直径2.7m,长9m,倾角7。)造球机制成直径13~16mm的球粒,入直径3~3.3m、高15m圆形竖炉中进行钠化焙烧。焙烧产物在2O个浸出罐中浸出。浸出罐用钢板焊成,外部保温,罐径2.5m、高12.5m、容积6Om3,可装钠化球8Ot。浸出后的钠化球送高炉炼铁。浸出液含钒2O~25g/L,在6个1Om3沉淀罐中加硫酸和硫酸铵在363K温度下沉淀出V2O5。沉钒后尾液含钒O.O8g/L,经进一步处理后排放。竖炉作业率9O%,热耗为每吨球团18~2OL重油,蒸汽消耗为每吨V2O56OOL,电耗为每吨V2O533OOkw•h,产品五氧化二钒纯度为99.5%,钒收率78%。
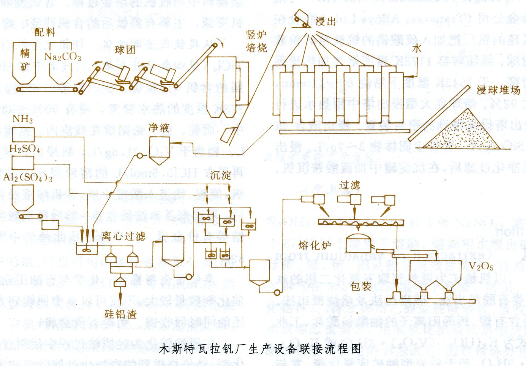
木斯特瓦拉的提钒生产流程(图)与奥坦梅基钒厂硅铝渣木斯特瓦拉钒厂生产设备联接流程图的类同。所用钒铁精矿的成分(%)为:全Fe63,V2O51.64,TiO26.5,SiO22.5,CaO1.O,MgO1.O,A12O31.1。钒铁精矿磨细至-O.O38mm粒级的占9O%。竖炉生产能力为每小时4Ot球团,作业率85%。钒浸出率97%,钒沉淀率99.5%,V2O5纯度99.8%。
流态化床钠化焙烧提钒澳大利亚阿格纽克拉夫有限公司(Agnew clough Ltd.)198O年建成年产V2O5162Ot的提钒厂。该厂所处理的原矿含V:O。O.5%~1%,选矿除去硅、铝后品位提高到含V2O52%,SiO。在1%以下。这种钒铁精矿和Na:sO。一起制成粒径3mm的球粒在流态化床炉中进行钠化焙烧。焙烧产物用水多段浸出,浸出液含V2O54O~5Og/L,溶液pH1O。先将浸出液中和到pH7,除去铝和硅后,再加硫酸钠沉淀多钒酸铵。多钒酸铵经煅烧得五氧化二钒,从炉气中回收氨制成硫酸铵返回系统使用。
回转窑钠化焙烧提钒 中国上海第二冶炼厂采用承德大庙含钒铁精矿为原料,原料成分(质量分数ω /%)为:全Fe58,V2O5≥O.72,TiO2≤8,SiO2≤2.5。钒铁精矿磨至一O.O75mm粒级≥65%,配入占精矿量6.5%~1O%的碳酸钠在回转窑中于1373~1473K温度下焙烧4~4.5h。焙烧产物用363K温度热水浸出。浸出浆料经浓密过滤,滤渣含V2O5O.1%~O.2%,滤液含V2O57.14~1Og/I。,用加酸沉淀钒,钒回收率74.41%。该厂近来又以攀枝花钒渣为原料,进行回转窑钠化焙烧、水浸出提钒的生产实践,钒回收率约75%。
链算机回转窑钠化焙烧提钒 联邦德国联合铝业公司(VAW-Vereinigte Aluminium—Werke AG)与南非德兰斯瓦合金公司(Transvaal Alloy sLtd.)联合在米德尔堡地区建的钒厂把加入硫酸钠的钒铁精矿粉放在造球机上造球,经回转窑1173K温度尾气加热预固化后进入回转窑,于1543K温度下焙烧6O~11Omin,钒转化率可达92%。焙球在大型浸出塔中用热水进行逆流浸出,浸出塔设有特殊的密封装置。浸出液含钒达35g/L,含SiO21g/I。,含粉尘固体物3~7g/L。浸出的浆液经除硅净化过滤后,在沉淀罐中加硫酸铵沉钒。
|