1前言 随着有色金属技术的发展,铝和铝型材加工以它特有的优势愈来愈广泛的用于航空工业和民用建筑、医疗、食品包装等行业。铝型材加工的热处理技术已发展成为热处理学科中的一个重要组成部分。 铝型材加工热处理包括:铝型材加工退火、时效、均匀化、固溶热处理等。随着铝型材加工产品的广泛应用,对铝型材加工热处理质量不断提出更高的要求,本文将对铝型材加工热处理技术的发展及关键问题进行综合分析和评述。
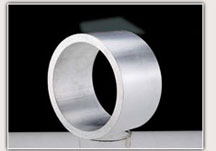
2铝型材加工的均匀化 在铝板带和铝型材生产工艺中,铸锭通过热轧、挤压可获得坯料铝卷带、铝型材。在铸造过程中,虽然可以通过在铝液中添加微量晶粒细化剂(Al-Ti-B)达到细化铸锭晶粒的目的,但铸锭的结晶组织还是不均匀。这是因为铝液的凝固是从结晶器的内壁开始,垂直于冷却面的方向向铝液内部扩展,所以铸造组织具有明显的方向性;随着铝凝固层的增厚,传热系数减小,内外晶核的形成和长大的不一致导致晶粒的形状、位向和大小也随之变化;凝固时金属成分造成的偏析现象,晶粒四周和晶内锰浓度的差异扩大了再结晶温度区间,降低生核率,从而容易产生粗晶;铸造时锭内部产生不同程度的缩孔和疏松组织。 在热轧、挤压过程中,由于热加工变形与再结晶同时进行,形成了以等轴晶粒为主的再结晶组织,可使铸造的结晶组织不均匀状态得到不同程度的改善。为了进一步改善热轧、挤压的性能,提高热加工后产品质量和档次,许多铸锭在热加工之前均在铝型材加工固相线下的温度570~620℃进行均匀化处理,使MnAl6相均匀析出,减小或消除晶内偏析,以达到均匀化之目的。 2.1 轧制用坯锭、卷带的二次加热和均匀化生产线 (1)推进式加热/均匀化炉 对于具有热轧能力的大型铝加工厂的批量生产来说,用推进式加热/均匀化炉来进行二次加热和均匀化比较合适。根据工厂的实际情况可采用加料和卸料的全自动操作或半自动操作,铝锭加热电炉。 4铝型材加工退火 铝型材加工退火分为板带材退火和箔材退火。退火的目的:消除冷加工硬化以便继续进行轧制或深度加工;控制产品的状态和性能;清除轧制油,提高表面质量。 根据生产能力和规模,铝材退火炉分为单体退火和退火炉群组成的退火生产线,见图6、图7。退火生产线一般由几台退火炉、复合装卸料车、炉外料台、冷却室(有些炉子带旁路冷却器)组成。炉体采用大风量风机对铝材进行循环加热,炉内的导流装置可有效保证气流均匀的通过铝材,使之加热均匀,加热器采用顶装整体式结构、拆装、维修很方便。炉门开闭采用气动压紧式或机械传动升降式,运行平稳,密封性好。炉子的排油烟系统可有效地去除铝材表面的油膜,调节炉内的压力。这种炉子的装料量一般为10~50t。 铝材退火炉是铝型材加工热处理中最广泛采用的设备。随着技术的发展和对产品质量要求的提高,对铝材的退火提出了更高的要求,如退火产品的外形质量、性能指标的一致性。 外形质量包括起皮、气泡、油斑、氧化腐蚀、表面光洁度等。内在质量包括力学性能、晶粒度、各向异性等方面。除退火工艺和设备外,产品退火以前的加工历史,如配料成分、熔铸工艺、冷加工率等,对退火产品的内在质量也有重要影响。 为了提高退火产品的质量,在炉膛气氛、炉温控制、炉型等方面需要采取改进措施。 ①对某些特殊要求的退火产品,可采用氧和水分含量极微的保护性气体作为退火炉气氛,以防止轧制油分子在挥发过程中裂解,产生碳氢化合物及游离的微小碳粒,在产品表面产生油斑;同时可减少表面氧化膜的厚度,使产品退火以后基本保护原有的金属光泽。 在使用保护性气体时,先将炉加热到150℃左右,装料后充入保护性气体进行洗炉,然后升温。在升温期间,产品表面油膜挥发,并从排烟口排出,同时补充保护性气体,以维持炉膛正压。待油膜全部挥发后,进行高温加热和保温,使产品在较短时间内再结晶,然后降温出炉。 ②真空退火是比较新的铝型材加工退火技术,可以防止轧制油分子裂解、氧化和聚合,在真空退火时,先将炉子抽到一定的真空度,然后加热,在加热过程中需要充入少量保护性气体用于驱除油气,减轻真空泵的负荷,并加速热量的对流传递。在冷却开始阶段,需要充入比正常运行更多的保护性气体使炉膛保持微负压或正压,通过对流风机和冷却器快速将炉子冷却下来。真空退火炉的密封要求严,真空泵容量大,对设备的要求较高,一般用于电解电容器的高纯铝箔退火。 3.1 立式炉(底装料) 该炉型适用于小批量、多品种的铝型材加工板材、型材、铸件的生产。一般采用高架式炉型,移动式淬火槽车,炉门采用两半对开式结构,工件在炉内采用悬挂式加热,倍行程滑轮组或卷扬机能使工件快速下降,确保所需的淬火转移时间。炉子的循环加热系统和温控系统确保淬火加热时温度均匀。该炉子和时效炉配在一起可形成淬火时效生产线(强化热处理),也可多炉组排列,共用一台淬火槽车。该炉型由于技术先进、操作灵活,目前应用比较广泛,但在设计中应特别注意以下方面: ①炉内温度均匀性 固溶热处理的特点决定了必须重视炉内温度的均匀性。选择固溶热处理温度必须考虑防止出现过烧、晶粒粗化、包铝层污染等弊病,尽可能采用较高的加热温度以使强化相充分固溶,但固溶热处理温度有一个高限和一个低限,如果温度过高,合金中的低熔点组成物(一般是指共晶体),在加热过程中发生了重熔(过烧);如果温度过低,强化相不能完全固溶,而影响合金的强度。因此在热处理规范上规定了固溶热处理温度的均匀性,要求在±3℃内。 固溶热处理的传热主要是依靠对流,因此炉内气氛的强制循环对同一批炉料实现迅速而均匀的加热,以达到要求的温度均匀性是首要条件。其它影响炉温均匀性的因素还包括循环风量的大小,循环次数的多少,以及循环气流如何均匀地流过工件,导流系统的良好设计,保温材料的选择等。 ②保温时间 固溶热处理加热时间首先与合金性质、原始状态有关。因各种铝型材加工的成分相似,所以对此不需特殊考虑,那么重点考虑的就是原始组织状态。当强化相比较细小时,因固溶较快,加热时间可缩短。例如冷轧状态的板材所需加热时间较热轧状态的短,重复淬火则更短,而一般退火状态因强化相较粗,保温时间应较长。另外,加热时间和加热介质、零件尺寸、批量等因素也有直接关系。 ③淬火转移时间 工件从出炉到进入淬火槽的间隔称转移时间,在转移过程中,工作温度下降可导致固溶体发生部分分解,从而降低时效强化效果,特别是增加合金的晶间腐蚀倾向。工件出炉后的温度降低5℃,可导致强度下降20%,为此,在生产中应尽可能缩短转移时间,尤其对热容量低的薄板来说,更为重要。一般淬火转移时间为7~25s,视工件大小薄厚而定。 ④淬火冷却速度 由于铝型材加工中合金成分的溶解度随着温度的降低而急剧下降,所以铝型材加工固溶体在淬火状态下处于过饱和状态,这样便可以实现时效硬化。根据铝型材加工的等温分解曲线,为了避免过量固溶体产生任何沉淀,在淬火过程中,铝型材加工件从固溶加热温度应快速降到300℃左右,为达到理想的效果,应保证足够的冷却速度。淬火介质通常采用水或者聚二醇。为减少变形和内应力,水温一般为20~50℃。 3.2 卧式铝型材加工固溶热处理生产线 这种生产线适用于大批量作业。典型的生产线有:连续铝型材加工锻件、铸件固溶和时效(沉淀)热处理生产线、悬浮式铝型材加工带材固溶热处理生产线、铝型材加工中厚板固溶热处理生产线。 悬浮式固溶热处理生产线可以处理0.2~2mm厚的带材,带材在通过加热炉时浮动在热空气垫上,不与炉子接触,以避免在带材表面留下划痕。带材在离开加热炉后立即淬火,淬火在一个气液两相冷却系统中进行。淬火介质采用水和空气,生产线上还备有热空气干燥器,保证带材热处理后完全干燥。 中厚板固溶热处理生产线原理上与立式固溶热处理炉相似,但当大批量生产时提高了生产效率,降低了能耗。具体工作程序为:采用真空吸盘将铝板放在装料台上,根据合金牌号和板厚的不同,板材或连续通过加热炉,或借助炉底辊的摆动在加热炉内加热之后进入淬火区和干燥区,最后到卸料台,再由真空吸盘卸下。 连续卧式铝型材加工固溶热处理生产线有如下关键技术: ①喷射加热技术 在加热炉内铝板由上下分布的空气喷嘴系统进行快速均匀地加热,喷射速度为30~70m/s,加热速率为1mm/min,喷射加热与其它加热相比可以提高传热系数,达到快速升温的目的。同时,均匀排列的喷嘴和精确地空气导流可以得到最小的温度允差。为了达到最佳效果,要合理设计喷嘴的角度、排列、大小和多少;高温高压高流率风机,精确的循环系统以及特殊的密封系统。 ②喷射冷却技术 为了使固溶热处理效果更好,卧式炉采用喷射冷却技术代替立式水槽淬火。主要特点是高压大流量喷水系统是喷射冷却的主体,移动式喷嘴可满足不同尺寸规格铝板淬火的要求;上下喷嘴与铝板之间的距离,水和铝板的接触点位置,上下喷水的一致性,喷嘴的形状、角度等是能否保证铝板快速冷却、冷却变形小的关键。 ③传动技术 连续固溶热处理铝板的最关键技术就是如何保证在整个热处理过程中,铝板不划伤,无压痕和镶嵌物,保持铝板的表面光滑。传动刷辊既可保证铝板表面质量,又可保证铝板与辊子之间有热空气流动,铝板任意点加热均匀。另外,分段传动时的变频调速、摆动传动、伺服同步传动等都是影响铝板表面质量的关键因素。 在设备的组成上,均热生产线一般由多台均热炉、冷却室、装卸料台、复合装卸料车、电控系统组成,采用电加热或火焰加热。在结构上和操作上虽然与前面所述周期式均匀化炉有很多类似之处,但为了保证圆铝锭的各项热处理参数,同时也是为了达到某种热处理形式所要求的效果,在设备的设计上还需要注意以下方面: ①热处理能力 如何合理的利用空间,最大限度的发挥炉子的热处理能力,这是炉子优化设计的主要内容。通常用于挤压型材铝锭的品种规格比较多,直径从85~400不等,一般来说,对于同一种均热炉,铝锭的直径愈大,长度愈长,装炉量愈大,生产能力也就愈大。为了合理安排产量,首先我们要了解产品的生产大纲和规格,既要考虑炉子的生产率,又要考虑炉子的使用率,同时兼顾炉子的规模、造价和成本。在一种炉型上兼顾处理长棒料和短棒料两种料时,合理安排装炉量更显得尤为重要。 ②均匀化时间 这是工艺问题也是生产能力问题。均匀化时间根据铝型材加工牌号而定,一般为4~6h(不含升温时间)。小于这个时间,会造成产品晶粒不均匀,型材的性能出现质量问题,影响成材率。大于这个时间,会造成二次晶粒长大和生产能力降低等问题。 ③冷却 铝锭均热后冷却有两个目的:第一是快速降温,提高炉组的生产率;第二是改善铝锭的挤压性能。由于铝锭的挤压性能受冷却速率影响甚大,因此要根据铝锭的品种、长短配备不同类型的冷却设备,以满足各种铝锭均匀化的需要,冷却通常分为水冷、气冷和水气混合冷却。在冷却过程中,既要保证铝锭快速、均匀的冷却,又要减少铝锭的变形。冷却速率的控制很重要,可以采用喷射冷却反馈技术,通过流量、压力和温度的反馈控制达到上述目的。 ④复合装卸料车的转移与自动对位 铝锭均热生产线一般配备多台炉组和冷却室、装料台等,复合装卸料车可实现炉料在炉子、冷却室和装料台之间的相互转移。为了实现生产线的全自动化操作,要求复合装卸料车具有自动准确的寻址功能(自动对位)、防惯性功能和与炉子的连接功能。根据工艺要求,复合装卸料车可分为二维、三维和可逆复合装卸料车等几种类型,特点是炉外停放,减少炉子的能耗、一机多用、异地操作、简单方便、运行平稳精确。 周期式均热炉一般以炉组形式出现,采用复合装卸料车对每台炉子进行加料和转移,另外还需配备大型的翻锭机构,在实际操作时,由天车与翻锭机构配合,将铝锭转移到复合装卸料车上,然后由它向各炉子加料和卸料。炉子上配备有大风量的对流循环系统和先进的温控系统,保证铝锭在均匀化时各部位温度均匀,这种炉子一般装炉量为30~60t。 为了保证这种炉型铝锭加热后的均匀化效果,必须有效的控制固相线下温度、温度均匀性和均热时间。因炉体温度相对退火炉较高,所以对风机的材质提出了较高的要求。另外,对循环系统、炉门密封和防止变形、炉内支撑受力的状态等,也是我们在结构设计上重点考虑的问题。 2.2 挤压铝锭的均热生产线 为了进一步提高铝型材加工型材的内在质量,使产品上档次,铝锭挤压前都采用均匀化工艺(均热)。由于铝锭规格和品种的不同,分为短锭均热和长锭均热两种,短锭一般为600~700mm,采用料筐装卸;长锭为(6~8)×103mm,每排料间由料垫隔开。根据型材的要求,圆锭直径从 85~ 400不等。铝棒均热炉如图3所示。 在这种炉子的操作程序中,坯锭被放置在加料辊台上,自动对齐后由翻锭机构将坯锭翻起在垫块上(也称为热靴),沿滑轨向前推进。推进是由液压推料装置将坯锭推送过炉膛,由于这种炉子多数是连续作业,推料装置与出料装置同步进行,推料装置受出料端的温度检测信号控制。 该炉可以采用电加热、气体或油燃烧器进行直接加热,通过大功率轴流风机进行空气循环,确保坯锭快速、均匀的加热。温度均匀性一般要求在±(5~3)℃,如此小的温度允差使得坯锭在固相线下的高温均匀化成为可能。采用先进的智能化控温仪表或计算机对坯锭进行差温加热,缩短了均匀化的时间。 推进式加热炉一般由进料翻锭装置、推料装置、炉体、加热系统、空气循环系统、出料翻锭装置、换气系统、温度控制和检测中心、料垫自动返回系统组成。 推进式加热炉的关键技术: ①热靴(料托):根据坯锭形状的不同,热靴的形式也有所不同,有分离型、组合型和整体型等。热靴的选型对坯锭在进出料、推进和加热过程中举足轻重,热靴的返回系统设计也不可忽视。 ②温度均匀性以及进出料协调:选用恰当的循环方式和导流系统会改善温度的均匀性。如针对不同的坯锭采用立式或卧式风机装置,或在风道中适当增加导流片来保证气流在炉膛内均匀分布。如何保证坯料在达到轧制温度后适时出炉,温度检测和反馈控制是很重要的。为了准确地反映和控制出料的时间,保证进出料动作的协调,设备的结构和重要部件的设计起着关键作用。 (2)周期式均热炉 考虑到加热各种品种和规格合金铝锭的需要,周期式均热炉要比推锭炉更适合生产的要求。周期式均热炉可装卸不同品牌、不同规格的合金锭,根据合金锭不同的工艺要求,将它们加热到相应的轧制/均匀化温度。该种炉子使用灵活、适应性强、可靠性高。铝扁锭均热炉如图2所示。 44t铝卷退火生产线 44t铝卷退火电炉卧式炉35t铝棒均热炉3铝型材加工的固溶热处理 铝型材加工的基本热处理形式是退火与淬火时效。前者属于软化处理,目的是获得稳定的组织或优良的工艺塑性;后者为强化处理,在淬火时使强化相充分地固溶在铝材中,在随后的时效过程中(又称沉淀硬化)获得最大的强化效果。因此,固溶热处理的目的是通过淬火过程形成起硬化作用的过饱和固溶体(起强化作用的合金元素),在固溶热处理时,通常将铝型材加工工件加热到500~570℃,然后以最快的速度冷却。 铝型材加工固溶热处理广泛用于航空工业的飞机蒙皮、壁板、框架、联接件等承力构件,以及汽车工业中汽车铝轮毂、发动机缸体、缸盖、活塞等受力部件。 |