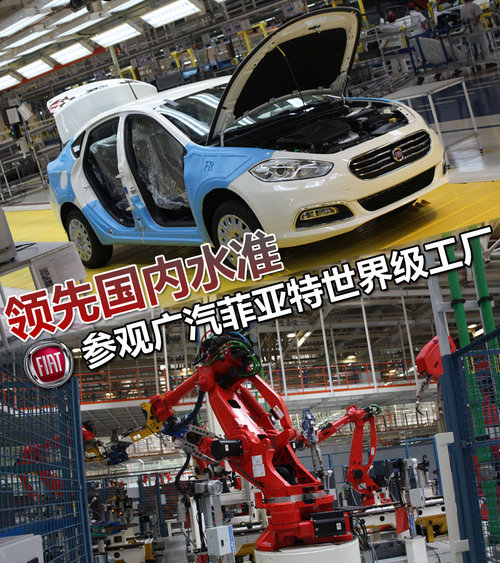
广汽菲亚特品牌首款国产轿车菲翔正式下线,新车将1.4T发动机匹配6速双离合变速器,将于9月正式上市,预计售价将在11万元起。在下线当天,我们也走入了菲翔的生产线-长沙广汽菲亚特工厂,参观了质量中心、换装车间以及总装车间,作为一款世界级的工厂到底会是什么样,接下来让我们走进这条生产线。
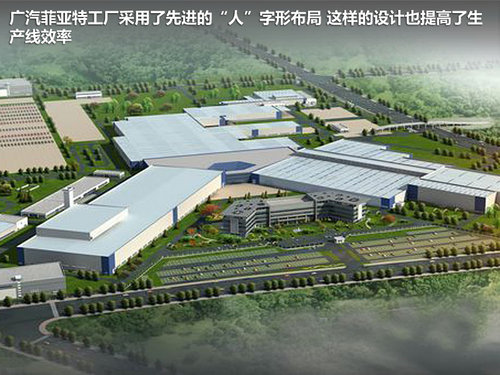
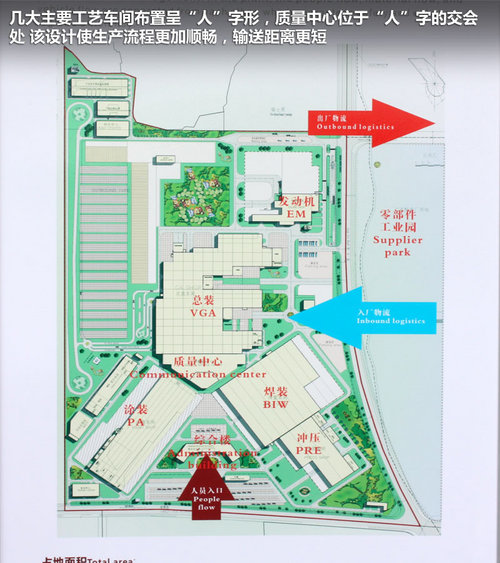
广汽菲亚特长沙工厂是菲亚特-克莱斯勒集团在全球的最新一家工厂。该工厂位于湖南省长沙市经济技术开发区,占地面积超过70万平方米,总投资额达50亿元,历时26个月建成,预计一期产能达14万辆,二期(2015年)年产能达25-35万辆整车。工厂采用了菲亚特-克莱斯勒集团WCM生产系统,以尊重自己、尊敬他人、尊重环境为核心价值观,拥有先进的流程布局、先进的设备工艺以及先进的环保理念,是全球技术最先进、最以人为本的中高级汽车生产厂之一。
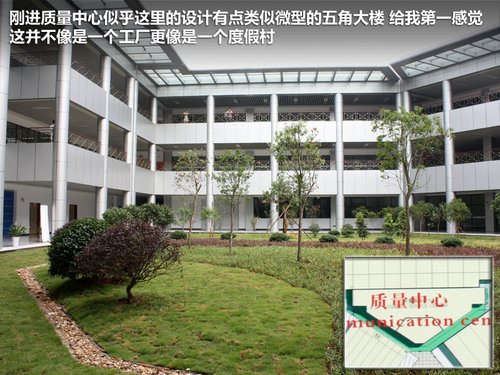
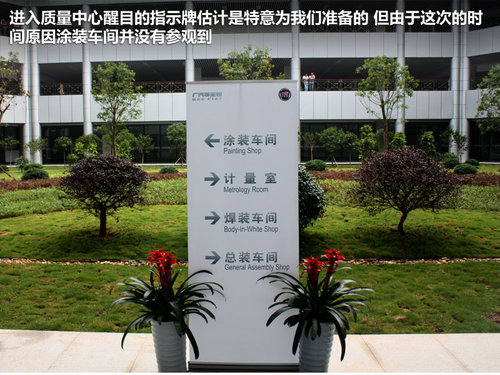
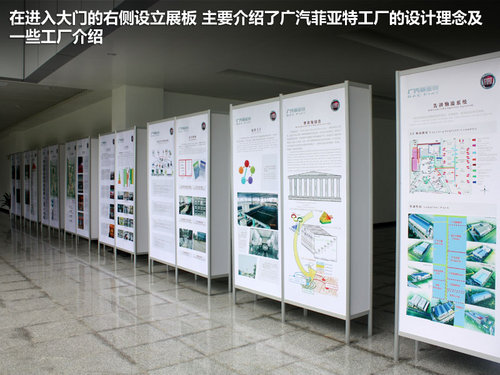
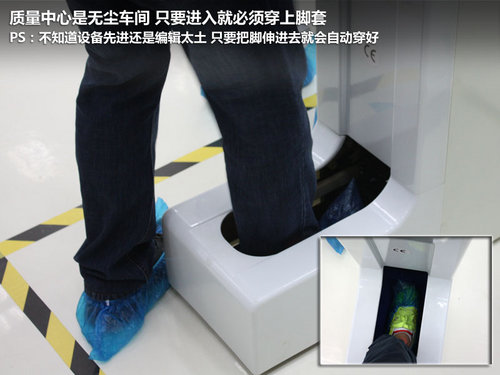
在现场的参观当中,记者也深深感受到了世界级汽车制造工厂的魅力。广汽菲亚特采用了多项世界先进的制造工艺和设备。这里采用了先进的“人”字形布局。几大主要工艺车间布置呈“人”字形,质量中心位于“人”字的交会处,该设计使生产流程更加顺畅,输送距离更短,同时也凸显了现场生产管理“以质量为中心”的理念。
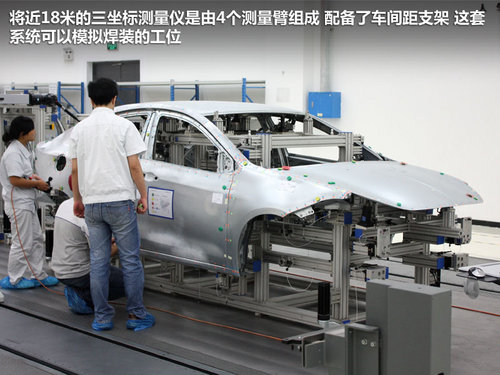
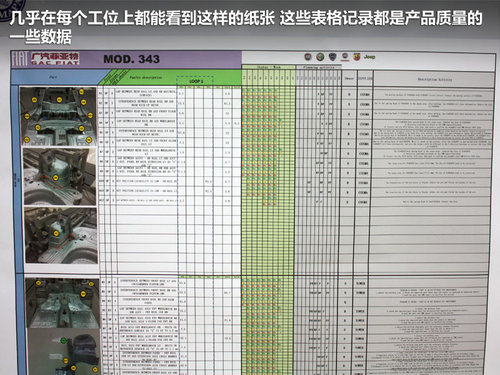
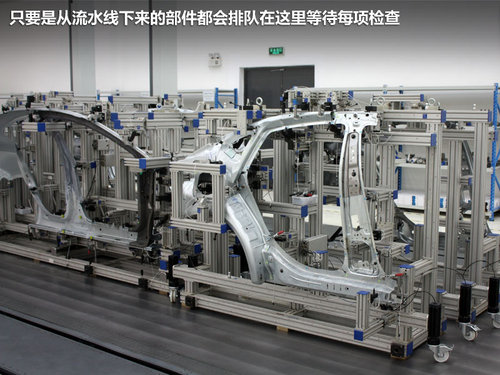
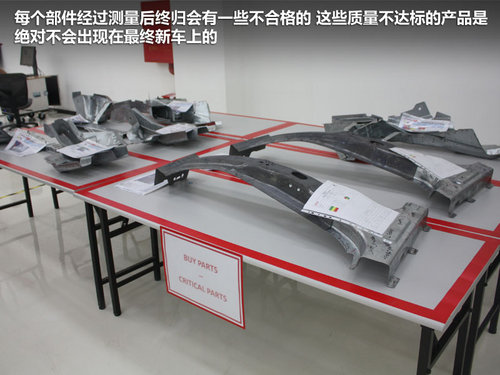
在进入质量为中心就能看到一台将近18米的三坐标测量仪,是由4个测量臂组成,配备了车间距支架,这套系统可以模拟焊装的工位。三维立体扫描通过拍摄图像进行输出,通过电脑可以对整个零件的轮廓进行精确的衡量。在对每个部件精致的测量后终归会有一些不合格的,这些质量不达标的产品是绝对不会出现在最终新车上的。
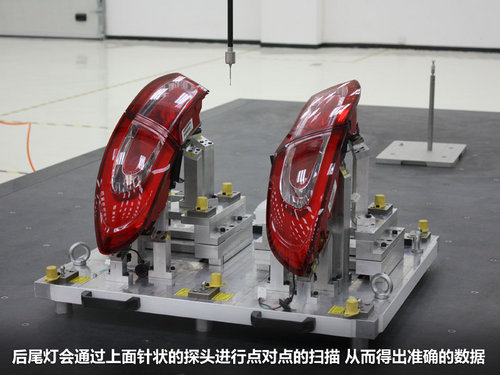
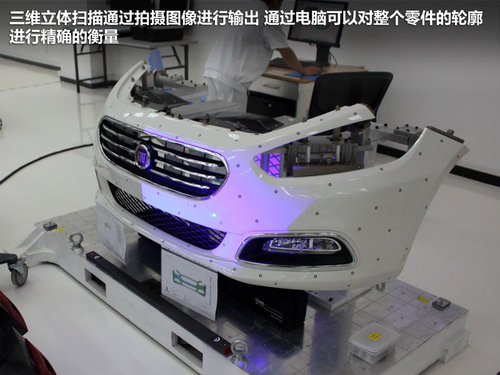
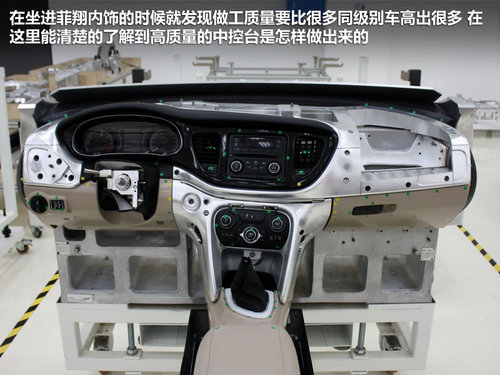
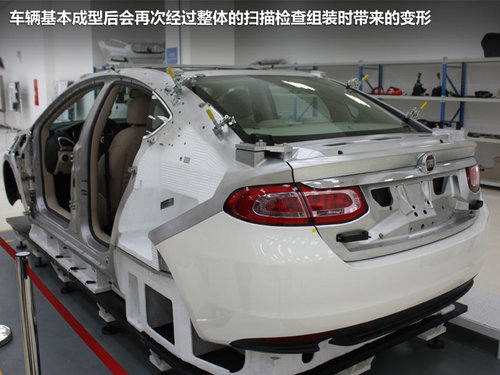
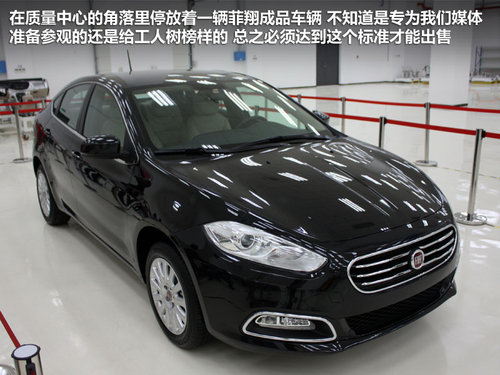
工厂内人流、物流、车流各行其道,零件配送、整车物流以及员工上下班路线的流向和距离得到有效区分,物流效率得以提升。而按照广汽菲亚特总经理郑显聪的说法,这样的设计还别有一番深意,那就是无论是谁,无论是哪个部门的员工,行进到质量中心的距离都是相等的,这寓意着“人人都平等”。
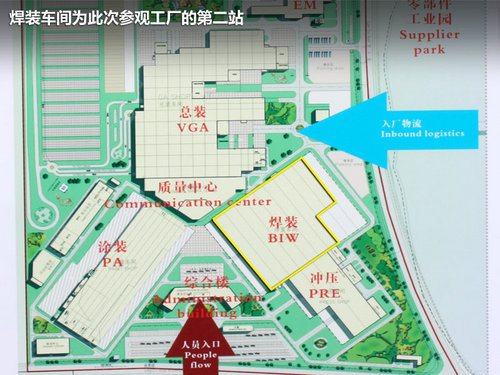
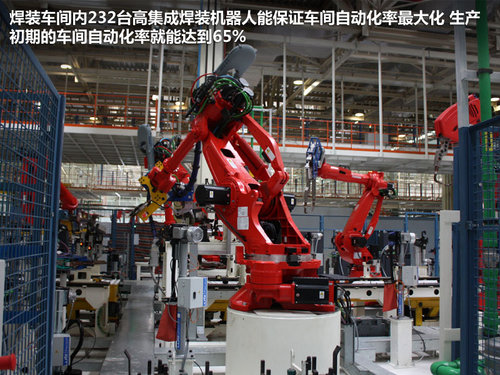
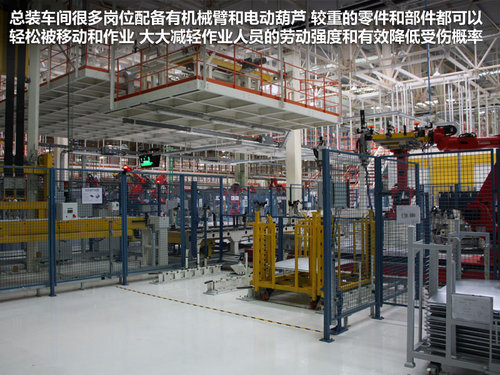
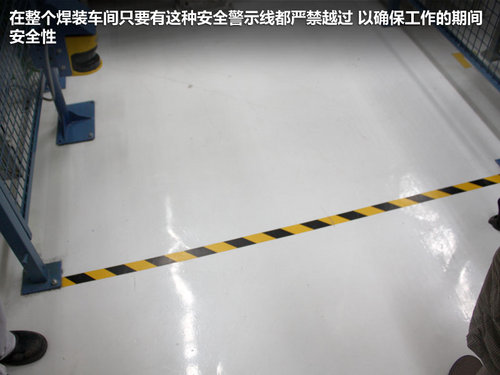
广汽菲亚特采用了多项世界先进的制造工艺和设备。焊装车间内,232台高集成焊装机器人能保证车间自动化率最大化,生产初期的车间自动化率就能达到 65%,车身顶篷激光焊接技术可使连接处车身刚度提高30%。总拼工位18台新一代机器人可同时工作,投产初期就能在92秒完成一台车身的焊接,并随着产能的提高不断提速。

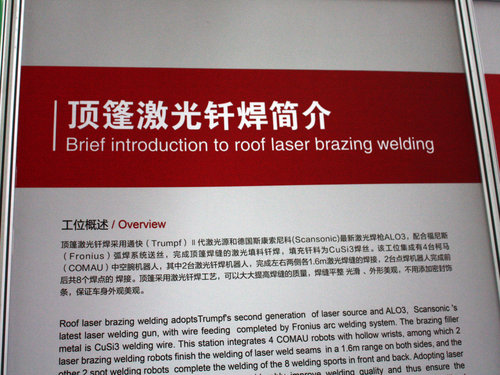
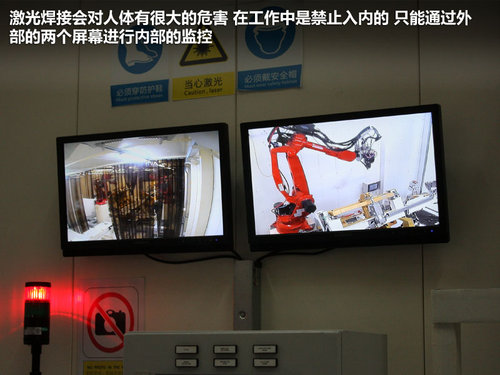
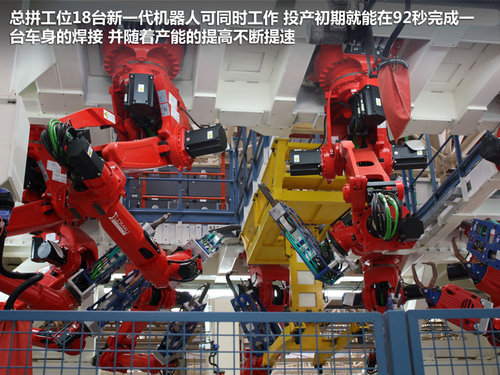
焊装线布局具有高柔性化的特点,能实现多台车共线生产。车间内采用了菲亚特最新底盘与车身合装工艺,实现高节拍下螺栓自动拧紧,该技术目前在国内处于领先地位。此外,广汽菲亚特是国内首家引进全套电器诊断设备和采用悬架震动实验台的厂家,前者确保各零部件总成在装车前的功能正常,后者消除车辆在下线时底盘悬架的各种应力,确保了底盘品质优良。特别值得提出的是,广汽菲亚特工厂所有厂房都配备了度量中心,确保最优秀的产品品质。
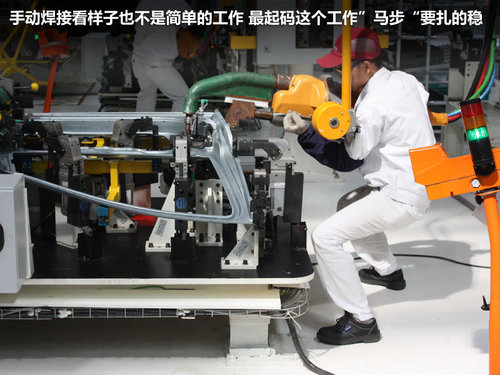
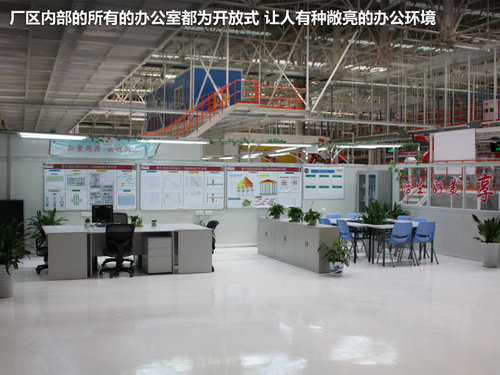

为确保产品品质,广汽菲亚特采用了世界先进的制造工艺。车身顶篷和门内板的激光焊接技术,提高了车身刚度,中频自适应焊接控制系统的焊机减少能耗50%以上;焊装线布局具有高柔性化的特点,能实现4款车型共线生产。臂挂式焊接机器人节省空间。车体空腔注入泡沫工艺,大幅降低车内噪音的同时,进一步提升了车身的刚度。E型布置的总装线和U型布局的发动机生产线,优化了物流管理,提升了生产效率。
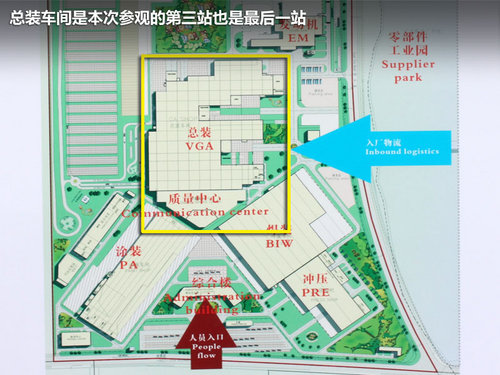
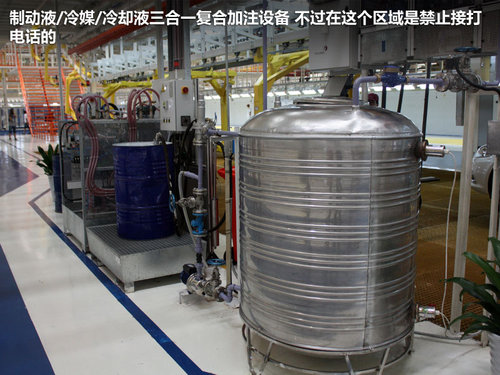
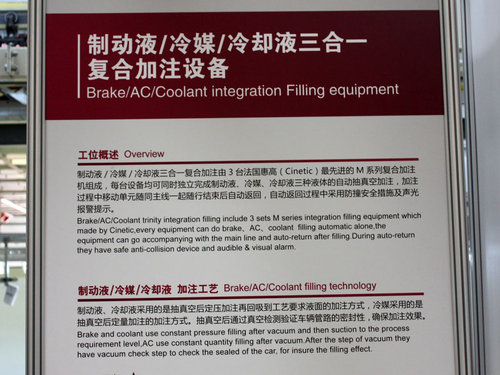
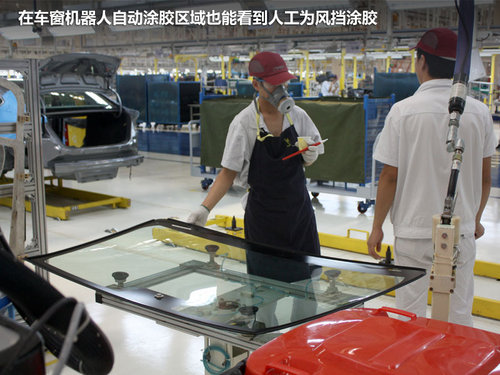
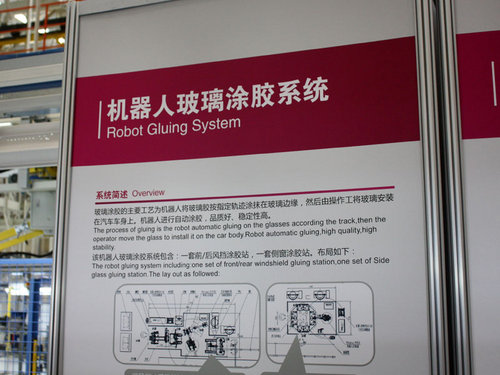
最后我们来到了总装车间,在冲压、焊装车间组装完毕的车体到涂装车间喷漆后由生产线运送到总装车间,进行发动机、底盘、内饰、外观部件的组装最后检验合格出厂。这个车间也是大家最感兴趣的,能看到平时根本看不见的零部件。
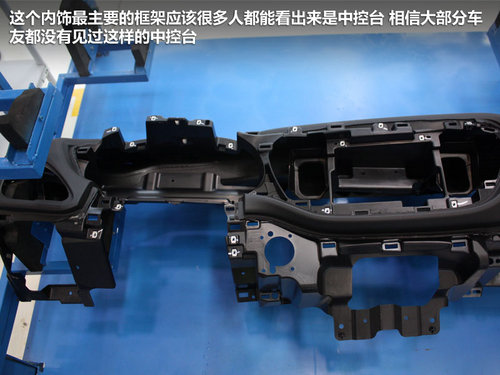
生产现场采用了一个流生产模式,即各工序只有一个工件在流动,使工序从毛坯到成品的加工过程始终处于不停滞、不堆积、不超越的流动状态。在广汽菲亚特的车间各类指示看板随处可见,各种颜色的汽车在流水线传送带上匀速移动,工序和工序之间按照作业排序实现了同步,均衡按节拍生产。
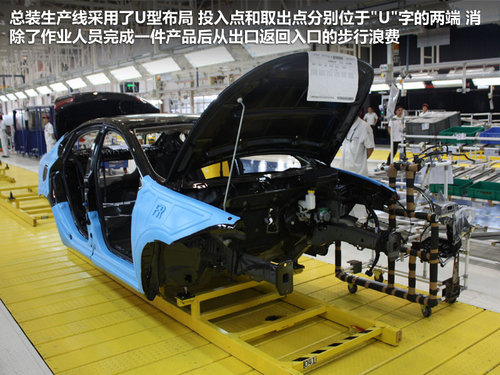
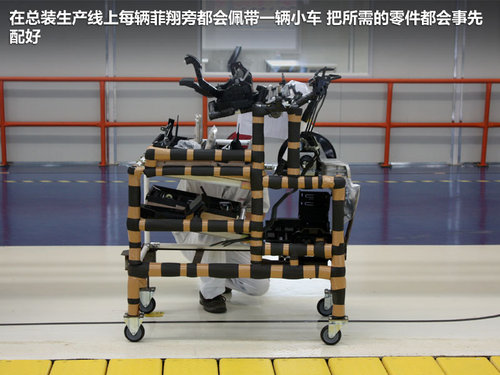
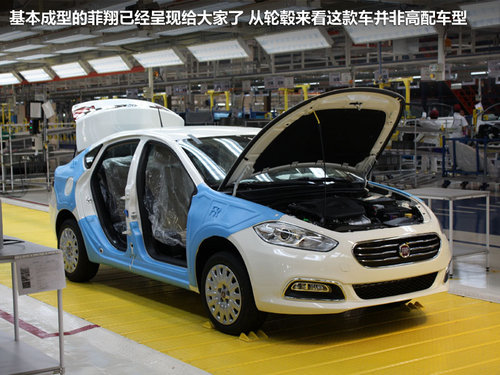
总装生产线采用了U型布局,投入点和取出点分别位于"U"字的两端,消除了作业人员完成一件产品后从出口返回入口的步行浪费。这样最大限度地节省了人力,保证了物流的通畅和消除了搬运、等待,在制品多等无价值的浪费。
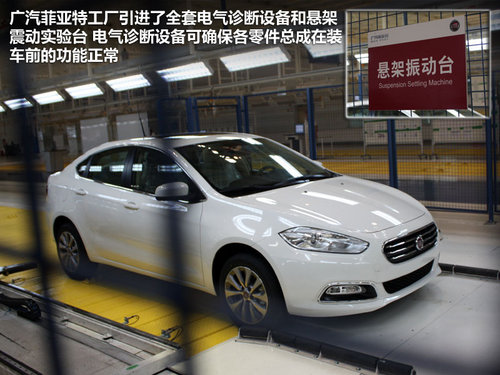
为了进一步控制品质,广汽菲亚特工厂引进了全套电气诊断设备和悬架震动实验台,电气诊断设备可确保各零件总成在装车前的功能正常,最终产品可靠安全。
由于时间因素制约,本次参观广汽菲亚特长沙工厂的行程非常紧密。走马观花式的游览,并不允许我将工厂中的更多信息收入眼中。但是在不到1个小时的时间中,我对于菲亚特新工厂的印象还是很深的。作为一个打算在中国重展宏图的品牌来讲,菲亚特的新工厂无疑给未来发展一个强有力的支撑。
(网上车市) |